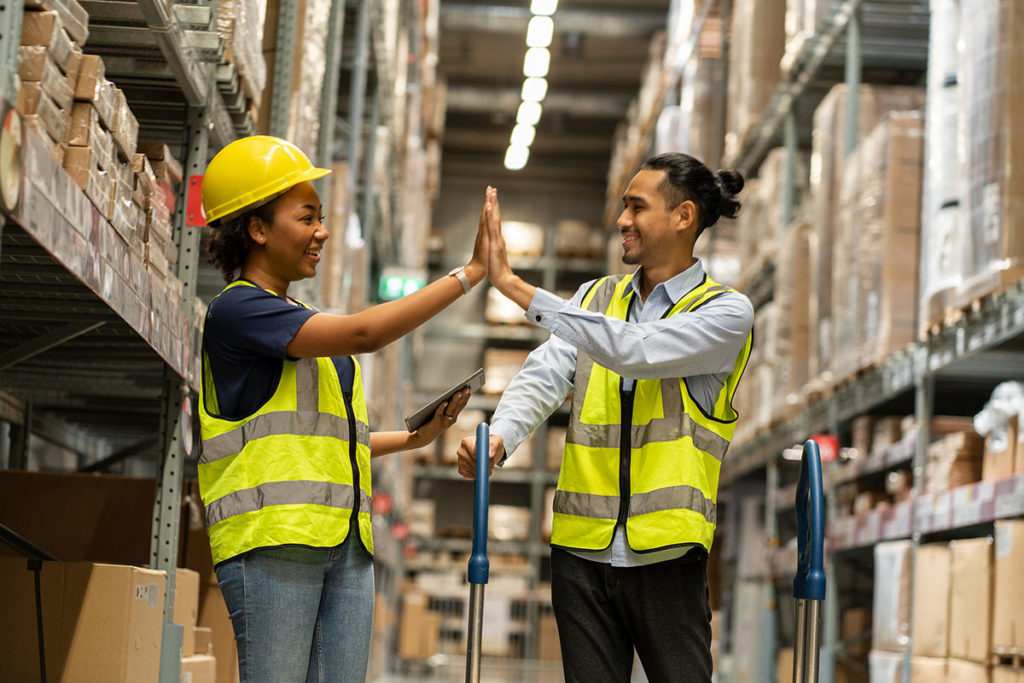
If you have been involved in manufacturing anything in recent history, you have been there – you have customer orders waiting, your lines are down, and you are just learning now that your components won’t be available for weeks, or even months, because of supply chain issues. That low-cost custom part could now hold up tens of thousands of finished good production units or even millions of dollars if it’s part of an Aerospace or Defense contract.
Could this have been avoided? Supply chains have been a hot topic with much focus on correctly planning demand, having alternate suppliers, and JIT inventory becoming a thing of the past. One more area of focus is available to ease supply chain bottlenecks and continue to supply cost-effective, on-time products.
The Design for Excellence (DFX) approach optimizes a product design to reduce total cost, increase manufacturing efficiency, and provide a better customer experience. It combines several modules, including Design for Manufacturing (DFM), Design for Assembly (DFA), and Design for Sustainability (DFS). With the onset of recent pervasive supply chain issues, the newest component to this approach is Design for Supply Chain (DfSC).
What is Design for Supply Chain?
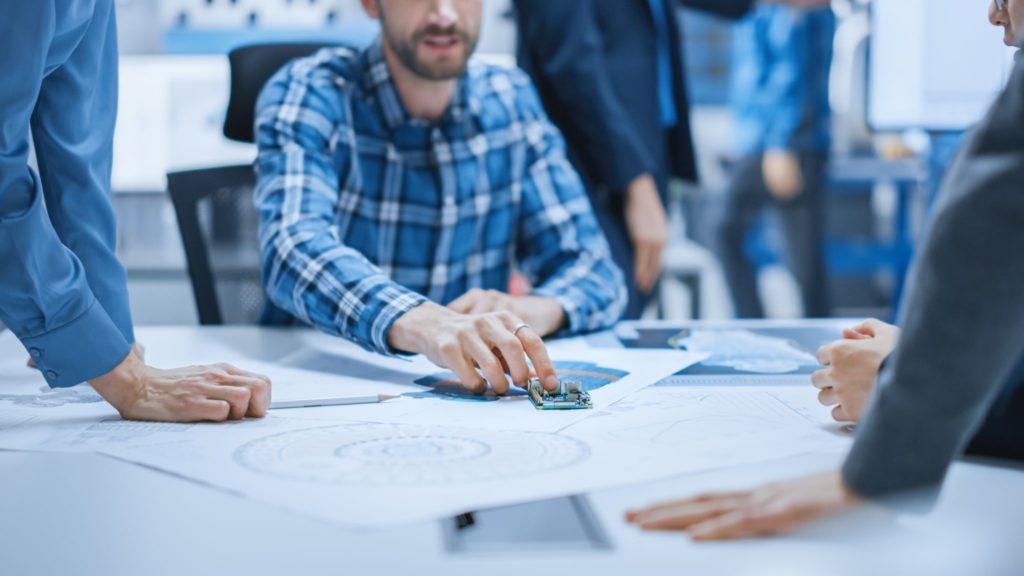
DfSC brings together a range of disciplines, including engineering, operations research, economics, business intelligence, process optimization, and data science. It uses a combination of data-driven analysis and collaborative decision-making between stakeholders such as suppliers, customers, logistics providers, manufacturers, and other partners in the value chain to ensure that materials are available when needed, transportation costs are optimized, and inventory levels are set appropriately.
This collaborative decision-making involves reviewing each component and considering the following:
- Is the component on the product development’s critical path, and what is the overall project impact?
- Are there standard parts available at or near the same quality and functionality?
- Can multiple common components be assembled to create a custom design feature?
- Would pre-assembling components at the supplier accelerate the process or cause additional supply chain complications?
- Are there multiple qualified and approved sources available for each material?
- Are there time/cost tradeoffs to be had between domestic and global suppliers?
- What are the costs/benefits of implementing design changes vs. accepting expedited freight costs on the original design?
Examples of DfSC Application
The questions outlined above can be applied at the beginning of product development or anywhere along the process when an impact to the supply chain is identified. A few recent examples of this process being applied during development at Nortech Systems are as follows.
Due to supply chain issues, a custom filter connector would not be available for several months. Their experienced team reviewed the design and identified a standard connector and filtered adaptor that, when combined, would meet functionality and space constraints. A temporary deviation was received from the customer, and production lines could continue until the original component was again available.
A similar situation arose with a 19 Conductor 22 AWG cable design. As specified by the customer, the lead time ranged between 6-9 months and would impact a downstream order on the customer’s end. The team reviewed each material and specification detailed in the original design and found an alternate cable, readily available, that met 80-85% of the requirements as specified. The alternate was suggested to the customer, who then did their own analysis to determine that it would be an acceptable alternative.
Having an experienced team who can not only analyze the design for alternatives but is also aware of current conditions or arising situations with material suppliers and can identify potential supply chain hotspots before they occur has countless benefits.
What are the advantages?
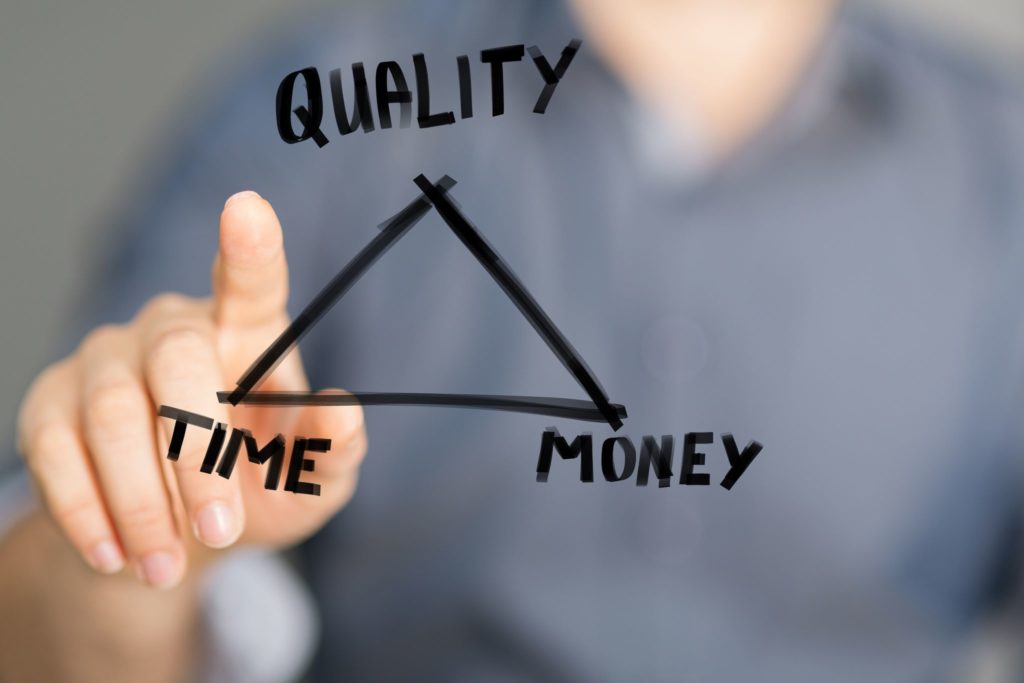
By creating greater visibility into all aspects of the supply chain, potential issues can be identified quickly and addressed before they become significant predicaments. However, capturing and quantifying the advantages afforded by these DfSC methodologies then becomes quite challenging since this proactive approach avoids potential issues before they become major, costly, measurable problems. That doesn’t mean a cost/benefit can’t be assigned to the work, but it may take a bit more for it to be appreciated.
The benefits of applying these methods after a product is released for production and then having a supply chain issue arise can always quickly be quantified in terms of time and dollars, as depicted by the above application examples.
Analyze your design with the experts
The real advantage of DfSC comes from working with experts in the cable, PCBA, and interconnect fields. Nortech Systems’ vast array of experienced engineers, technicians, project managers, supply chain managers, demand planners, and inventory control specialists focus their trained eyes on your design, manufacturing process, and supply chain. By understanding your application, they can recommend more straightforward and cost-effective solutions that will help you balance risk mitigation and cost. They understand wire and cable better than anyone, allowing you to focus on your application and leave the tail-end interconnectors to their experts.
Design for Supply Chain considers the complete life cycle of an engineered product from concept through delivery, recognizing that modern supply chains necessitate creating products with a broad range of stakeholders in mind. In effect, DfSC enables you to consider not only how a product is designed and assembled but also how it is manufactured, shipped, stored, maintained, refurbished, and recycled/reused when it reaches obsolescence – all while achieving budgetary targets.
Although the effects of the pandemic on the supply chain are slowly receding, domestic and global labor shortages are not and will continue to affect material availability. Contact the experts at Nortech Systems and add DfSC analysis to your product development and production plans.