In today’s fast-paced electronics industry, protecting delicate PCBAs and cable assemblies has become a vital requirement for manufacturers. Low-pressure molding (LPM) has emerged as a favored alternative to traditional overmolding methods. This innovative molding process ensures the protection and integrity of sensitive components while offering efficient solutions. To achieve optimal results, it is important to keep in mind the following key considerations when designing with this cutting-edge technology.
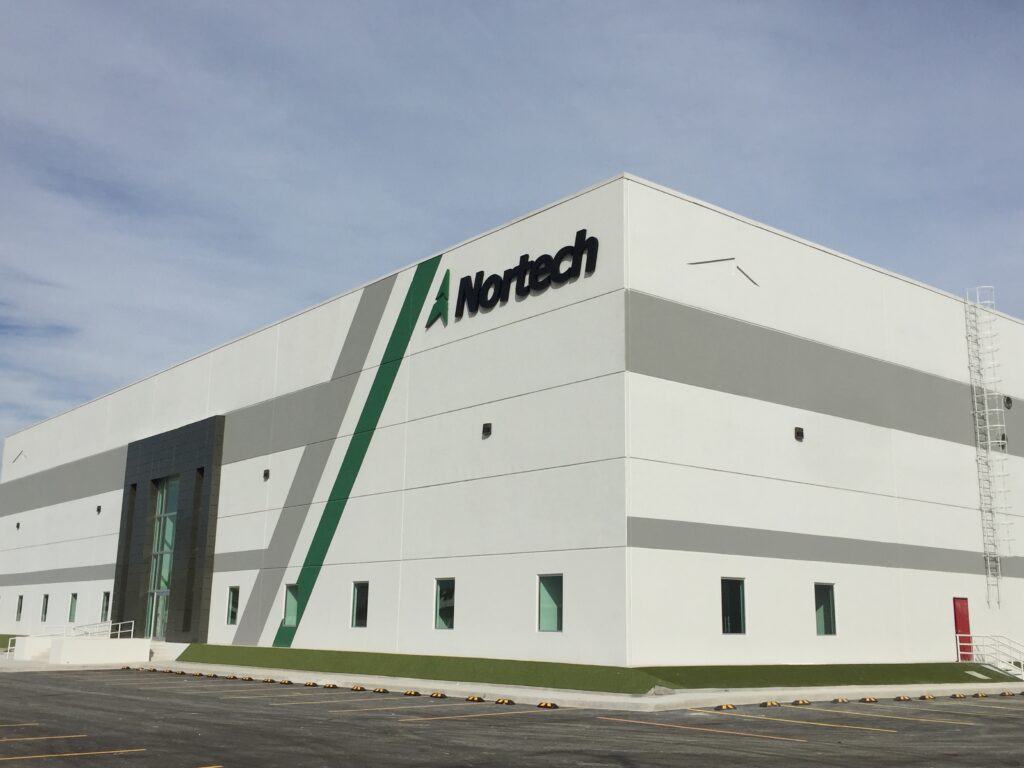
Understanding the Benefits of Designing With Low-Pressure Molding:
Before delving into key considerations, it is essential to comprehend the benefits of low-pressure molding to determine if it is a suitable solution. Compared to traditional high-pressure injection molding, low-pressure molding provides numerous advantages.
Unlike other potting methods, LPM utilizes a thermoplastic, hot melt adhesive with uniquely low viscosity, making it moldable in a low-pressure environment. This characteristic is particularly crucial for backshell manufacturing, especially when dealing with fragile electrical components that could be damaged by high-pressure injection molding processes. Moreover, hot melt adhesives have excellent adhesion and sealing properties, making them ideal for weather-resistant applications. LPM provides waterproofing, UV protection, and increased durability for delicate PCBAs and cable assemblies.
Additionally, this process does not involve a chemical curing phase. Because of this, excess materials such as runners and scraps can be melted down and recycled for future molds. This significantly reduces waste and the overall environmental impact of the production process.
Consider the Application of the Component:
When considering the applications of an electrical component, engineers can design for a variety of unique environments. As previously mentioned, the unique characteristics of low-pressure molding allow fragile electronics to be designed for harsh conditions, significantly extending their operational lifespan. This is especially important in applications where components are not easily accessible or difficult to replace. Overmolds produced with the low-pressure molding process exhibit enhanced resistance to environmental factors such as moisture, vibration, and mechanical stress.
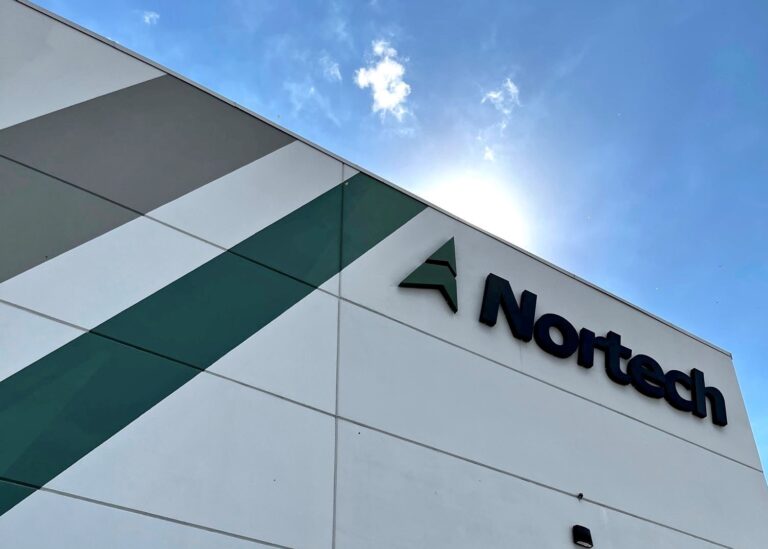
Consider the Shot Size of the Mold:
If the intended application requires high production quantities, the volume of hot melt adhesive used should be considered when designing with low-pressure molding. The shot size is a key factor when minimizing production time.
Decreasing the overall volume results in faster hardening of the thermoplastic, leading to reduced cycle time. Additionally, smaller shot sizes enable the simultaneous use of multiple cavity molds, facilitating higher-volume productions in less time.
Consider the Shape of the Low-Pressure Molds:
The shape of low-pressure molds is a critical consideration when developing a new component. While low-pressure molding offers unique solutions, the mold must be designed with the desired capabilities in mind. When designing a PCBA overmolding, engineers must ensure that they account for an overall mold size that is suitable to provide adequate protection. For example, if the mold is too narrow, the electrical component will be more susceptible to damage from flexing and stress. Similarly, cable attachments can subject the component to significant strain. Properly designed backshells can provide adequate strain relief to cable assemblies, and protection against mechanical stress. Ensuring the thermoplastic is of sufficient thickness and shape around these areas is crucial in preventing failure.
Low-pressure molding presents a transformative approach to manufacturing delicate and intricate designs while safeguarding sensitive components.
By understanding its benefits and considering the application, the shot size of the mold, and employing proper mold design, engineers can fully capitalize on the potential of this innovative technology. Embracing low-pressure molding not only enhances product durability but also offers a more environmentally friendly solution for higher-volume productions. With its ability to provide waterproofing, UV protection, and increased lifespan for PCBAs and small cable assemblies, this innovative technique is a versatile solution in the electronics manufacturing landscape.
As businesses strive for efficiency and sustainability, low-pressure molding emerges as an innovative solution in today's fast-paced industry.
At Nortech, we pride ourselves on our ability to provide comprehensive support throughout the design and manufacturing process. With a team of experienced specialists, we are well-equipped to navigate the intricacies of low-pressure molding and offer expert assistance at every stage. Whether it is helping work around design constraints, optimizing backshell design for component protection, or starting out from square one, our team is dedicated to collaborating closely with our customers to help meet their needs. From concept to production, Nortech is committed to delivering exceptional results and ensuring that interconnect components receive the utmost care and protection with our innovative low-pressure molding solutions.