In the world of electronics manufacturing, both white rooms and clean rooms play crucial roles, serving different purposes and following distinct standards. A white room is primarily designed to control factors like temperature, humidity, and dust. These environmental controls ensure the protection of sensitive electronic components during assembly and reworking processes.
Clean rooms take it a step further. In addition to managing environmental factors, clean rooms strictly regulate and limit the presence of particulate matter, such as dust, airborne microbes, aerosol particles, and chemical vapors. This level of control is vital in electronics manufacturing, where even the tiniest contaminants can lead to defects or product failure. Clean rooms adhere to the standards set by the International Standards Organization (ISO).
To put it simply, while all clean rooms can be considered white rooms, not all white rooms meet the stringent standards of a clean room. Rest assured, in both white rooms and clean rooms, utmost care is taken to ensure the quality and reliability of electronic products. Both are necessary in mitigating risks in all areas of electronics manufacturing.
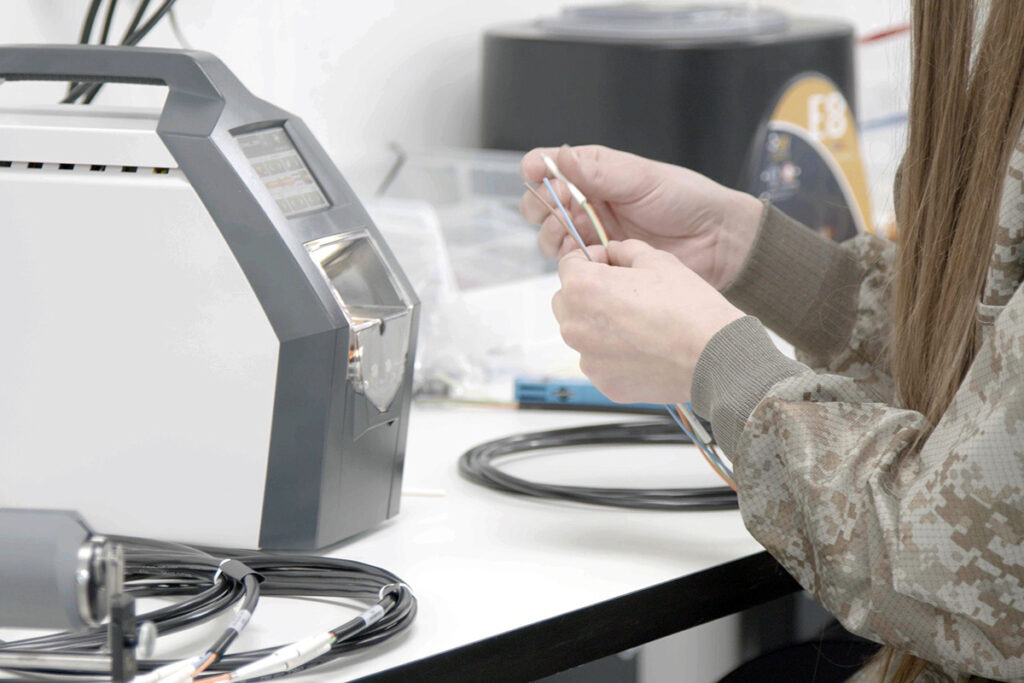
Clean Room Facilities Alleviate Particle Contamination on Connectors
Foreign Object Debris (FOD) encompasses any substance or object that has the potential to harm electronic systems. Even seemingly insignificant materials like dust or human hair can cause considerable damage, ranging from connectivity issues to short circuits, system failures, and component damage. To ensure reliable connections, it is crucial to maintain a controlled environment free of contaminants. This is where white rooms play a vital role in the manufacturing and handling of fiber optic cables. Particle contamination on connectors can scatter or absorb light, leading to weaker signals or failure within fiber optic assemblies.
Similarly, FOD poses a significant threat to mission-critical systems, where a malfunction can have catastrophic effects. Aerospace and defense systems rely on complex and delicate components, which must be manufactured, assembled, and tested in controlled environments that are free from contaminants.
White rooms provide the ideal conditions for the processing of these sensitive components and play a crucial role in mitigating foreign object debris. They enable precise manufacturing and assembly, which is essential in industries where even the smallest of particles can lead to system errors.
Mitigating Risks for Medical Device Manufacturing
ISO-certified clean rooms play a critical role in the manufacturing of medical devices. From PCBAs to high-level medical builds, these devices require the utmost precision and hygiene during production.
Maintaining high cleanliness standards in clean rooms is of utmost importance for medical device manufacturing. The stringent protocols and practices implemented are aimed at minimizing any potential sources of contamination, as even the slightest deviation can have serious repercussions on patient safety. For instance, the presence of harmful microbes in these controlled environments can significantly increase the risk of infections, compromising the well-being of patients and the overall efficacy of medical procedures. Therefore, ensuring thorough cleanliness and adherence to strict ISO requirements is vital in safeguarding the health and welfare of individuals who rely on these medical devices.
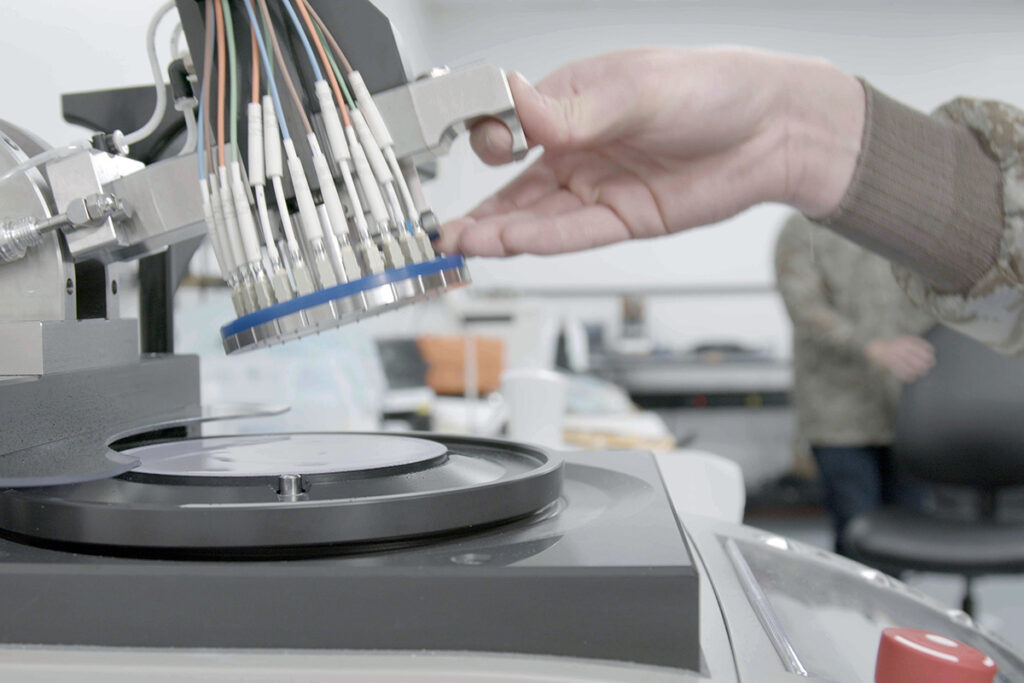
Nortech's Industry Leading White Room and Clean Room Facilities
Nortech’s clean room and white room environments are meticulously controlled to mitigate risks and ensure the integrity of the products we manufacture from fiber optic cables to medical devices and aerospace electronics. Our Nortech Milaca facility is ISO 14644-1 certified to meet the rigorous requirements of our medical clients. Nortech Bemidji facility’s white room also adheres to ISO 146441, class 8, and supports our client’s fiber optic needs. Our processes at both facilities underscore Nortech’s commitment to quality and safety.