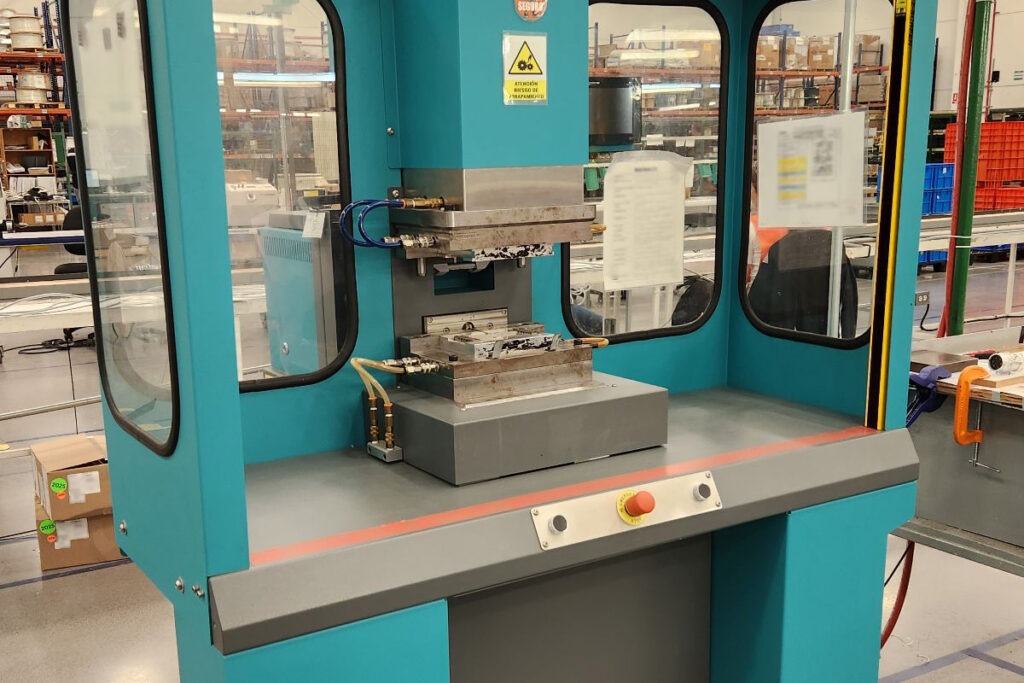
Cable assemblies are key components across industries, from medical, aerospace to military applications. Their reliability and protection from external elements can significantly improve the performance of connected systems. Cables with molded connector strain reliefs and junctions provide superior reliability to shrinkable boots and mechanical backshells. Molded assemblies are sealed for life and provide excellent strain relief, environmental protection, abrasion protection, shock and impact resistance, most often at lower cost.
The Fundamentals of Overmolded Cable Assemblies
An overmolded cable assembly integrates molded materials, typically thermoplastics, directly onto electronic components. This technique creates a seamless, durable connection that protects internal wiring from external environmental threats. The molding process involves enclosing the connector, cable terminations, or receptacles into a single, cohesive design. With the complexity of tooling increasing and the number of potential materials that can be used in the overmolding process growing, parts that are to be injection molded must be designed with careful consideration.
Low-pressure molding and injection molding are two methods used to produce overmolded cables, each tailored to specific applications. We’ll also explore two-part Polyurethane and why the Nortech team selects it to seal our assemblies.
Injection Molding at Our Bemidji Facility
Our Bemidji facility employs injection molding techniques for robust cable and connector production. Injection molding uses high-pressure systems to shape durable thermoplastics around internal components. This method is particularly advantageous for applications where longevity and hard-wearing assemblies are critical. Injection molding is created using thermoplastics which provide a sleek look. This overmolding material is melted and injected into the mold under high pressure. The heated material flows around the connectors, fills any gaps, creating a smooth, uniform mold. At Nortech, injection mold tooling is available for many D-Sub connectors and circular connectors. We also offer 3D printed mold tooling for quick turn prototyping and production.
Low-Pressure Molding at Our Monterrey Facility
At our Monterrey manufacturing facility, we specialize in low-pressure molding for overmolding fragile electronic components. This technology achieves durable, compact assemblies without subjecting delicate components like printed circuit boards (PCBs) to excessive pressure or heat. Compared to traditional overmolding which can be problematic for delicate parts, requiring extreme temperatures and pressures, low-pressure overmolding can be beneficial to safely encapsulating electronics into a molded part. This combination of precision and adaptability makes low-pressure molding an optimal choice for complex assemblies that prioritize performance and longevity.
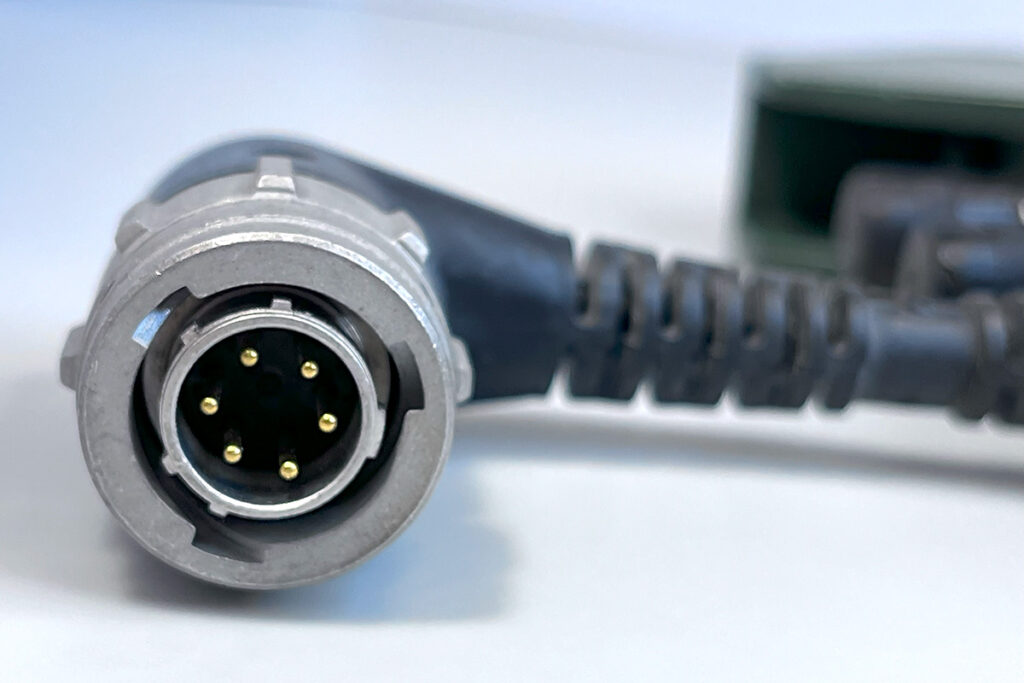
Two-Part Polyurethane for Military Applications
For industries like the military, where environmental resilience is vital, two-part polyurethane adhesive stands out. This solution is widely recognized for its ability to withstand extreme pressures and harsh conditions. Military-grade applications frequently demand exceptional sealing, abrasion resistance, and robustness, all of which this process provides.
- Superior Sealant Properties: Two-part polyurethane creates a secure barrier, protecting internal wire connections from water, dust, and other contaminants.
- Pressure Resilience: Polyurethane is ideal for high-pressure applications, including underwater environments such as submarines.
- Enhanced Longevity: Polyurethane’s abrasion resistance prolongs the life of cable assemblies, even in the most demanding scenarios.
Advantages of Molded Cable Assemblies
Understanding the strengths of molded cable assemblies can help engineers and manufacturers select the most suitable solution for their projects.
- Comprehensive Sealing and Protection:
Molded cable assemblies provide superior sealing to protect against moisture, dust, and contaminants. Unlike traditional backshell cable assemblies (which can be disassembled, exposing wires to damage), molded cables offer permanent encapsulation of wire connections. This makes them especially effective in environments requiring extreme durability, such as aerospace, industrial machinery, and military applications.
- Resistance to Abrasion and Environmental Factors:
Abrasion, high pressure, and temperature changes can severely compromise cable functionality. Overmolded cables excel in these conditions thanks to the resilience of molded materials like polyurethane and thermoplastics.
For example, in submarine applications, overmolded assemblies withstand underwater pressure while maintaining full functionality. This unparalleled durability ensures reliable performance in the most demanding applications.
- Simplified One-Piece Design:
Overmolded cables eliminate the need for additional backshells, mechanical fasteners, or gaskets. The seamless, integrated design reduces assembly errors, shortens production times, and minimizes maintenance. This streamlined approach aligns perfectly with industries that prioritize cost-effective and reliable solutions.
- Longevity Without Rework:
While backshell cables are serviceable and allow access for repairs, this can also lead to greater risk of damage and a reduced lifespan. Overmolded cable assemblies, being permanently sealed, offer protection that eliminates concerns of improper resealing after maintenance. Applications that require minimal to no disruption benefit tremendously from this robust design.
Innovation in Molded Cable Manufacturing
At Nortech, we are committed to advancing cable assembly technologies while maintaining quality and engineering excellence. Whether you’re creating assemblies for medical devices, industrial applications, or high-stakes military operations, we have tools, expertise, and technology to meet your needs.
Unlock Your Cable Assembly Potential
With the experience and equipment required to deliver quality molded cables, it can be a challenge to find cable manufacturers with technical knowledge and the tools to produce molded cable assemblies all in one house, but not impossible. If you are ready to enhance your operations with robust molded cable assemblies, Nortech is here to assist you from conception to production. Contact us today to discuss your project needs and discover how our expert team can elevate your manufacturing process.
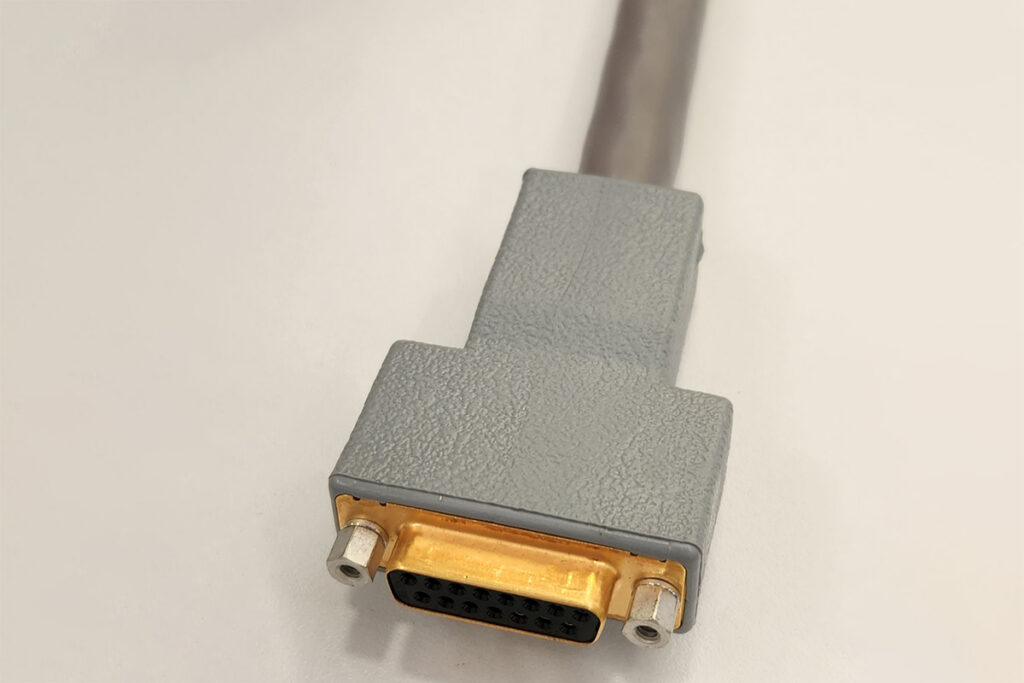