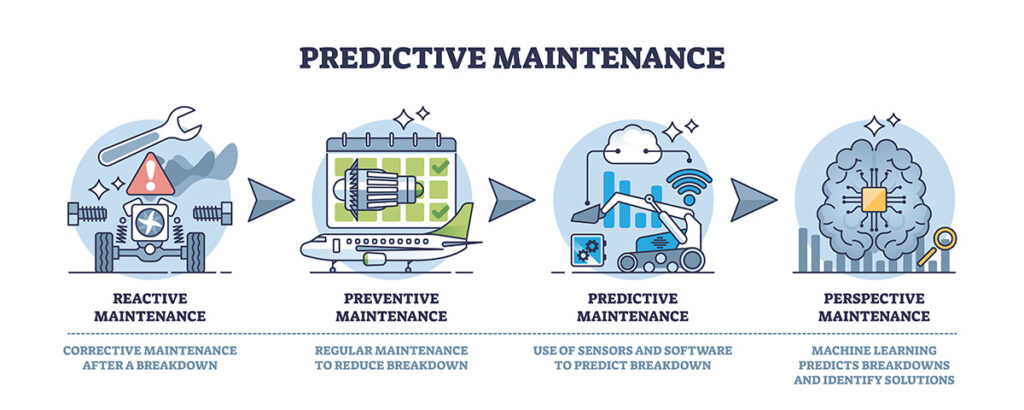
In recent years, the capabilities of manufacturers have undergone significant changes. Continuous advancements have led to a complex integration of physical and digital systems. This industry trend is commonly referred to as the fourth industrial revolution, or Industry 4.0. Furthermore, this transformation is driven by companies seeking to minimize waste and enhance the efficiency of existing systems. Advancements in artificial intelligence (AI) and machine learning (ML) have ushered in a new era of efficient maintenance practices.
Historically, manufacturers have heavily utilized outdated and inefficient maintenance strategies to ensure a consistent and reliable production process:
Reactive Maintenance:
This approach involves repairing systems only when a failure has already occurred. While simple, this method has major limitations. Relying on observable failures within the production process can lead to issues going unnoticed for a significant amount of time before they are addressed. This can result in prolonged periods of reduced efficiency or defective final products due to unnoticed issues. Additionally, this approach often leads to unplanned downtime for system maintenance. With reactive maintenance, even the smallest failures can have a significant impact on production schedules and cause delays.
Preventive Maintenance:
Another common method of equipment maintenance is preventive maintenance. This approach involves proactively scheduling maintenance based on regular periods or cycles. The primary objective is to prevent failures and ensure a consistent and reliable production process. However, it is important to note that this approach can sometimes lead to unnecessary maintenance, resulting in increased operational costs and reduced efficiency.
Machine Learning and Predictive Maintenance
Industry 4.0 and its associated technologies have revolutionized maintenance practices, offering a fresh approach. At its core, machine learning, a subset of artificial intelligence, leverages vast amounts of data to identify trends and draw inferences. With production equipment fitted with sensors, copious amounts of data on system performance are generated. By continuously monitoring this data, machine learning enables the prediction of system performance and degradation. These predictions serve as early indicators of potential system failures, enabling proactive repairs. This transformative practice, known as predictive maintenance, is reshaping the manufacturing sector.
Benefits of Predictive Maintenance:
Enhanced Efficiency
Predictive maintenance utilizes machine learning to effectively manage complex and multivariable data sets, enabling the identification of areas of inefficiency within manufacturing processes.
Reduced Downtime
By pinpointing areas of degradation, manufacturers can prioritize and schedule maintenance to minimize its impact on the production process.
Lower Operational Costs
Automated system monitoring prevents costly and unnecessary maintenance procedures, resulting in reduced operational expenses with minimal human intervention.
Improved Quality
Continuous monitoring of system health ensures that products are manufactured according to design specifications with high precision.
Predictive maintenance is made possible by continued IIoT integration within the realm of industry 4.0. The effectiveness of the insights derived from machine learning is directly proportional to the abundance of available data. By utilizing IIoT-enabled devices and sensors, a comprehensive understanding of every stage of the manufacturing process can be achieved.
Ensuring a robust and properly implemented smart-enabled infrastructure is of utmost importance for organizations to fully capitalize on the advantages offered by this digital transformation. Smart cable technologies are becoming more crucial in enabling efficient smart factory operations. By integrating sensors into these cables, real-time monitoring of cable and system conditions is possible. When combined with machine learning algorithms, this data can be leveraged to anticipate maintenance requirements or determine when replacements are needed. Additionally, these cables facilitate the seamless handling of large volumes of data and power, essential for accurate predictive maintenance.
At Nortech, we are deeply committed to supporting and promoting the adoption of cutting-edge predictive maintenance practices. We provide our customers with innovative IIoT and interconnect solutions, along with efficient data management tools. Through our comprehensive and industry-leading offerings, we empower businesses across various sectors to optimize their operations, minimize downtime, and achieve unprecedented levels of efficiency in their maintenance processes. By leveraging our expertise and staying at the forefront of technological advancements, we ensure that our customers stay ahead in the rapidly emerging field of predictive maintenance.