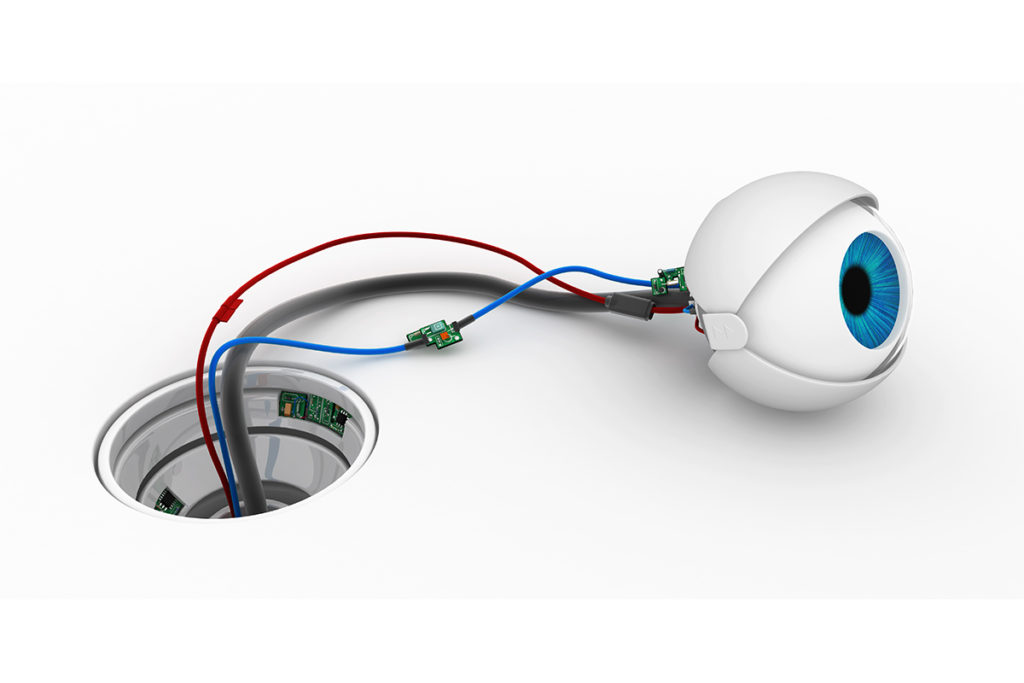
Vision and sensor systems are rapidly requiring better, more reliable data transmission, and more of it across longer distances at faster speeds. The manufacturing trends towards smart factories, increased use of robotics, and more and more machine vision applications within those industries are driving this demand.
Current commodity cables fall short of keeping up with these advancements as they may be inexpensive, but they are typically limited to transmitting data across no more than 10 meters, have poor reliability, and frequently fail in an industrial environment.
Multi-function cables, such as the hybrid model developed by Nortech Systems, combine copper and fiber with a USB-C connection to form a hybrid active optical data cable. This combination yields a streamlined solution with enhanced power delivery, designed and tested for rugged environments.
Read on to learn more about today’s current manufacturing trends and how multi-function cables will meet the rising capabilities demands.
Smart Factories
In recent years, there has been a growing trend among manufacturers to adopt “smart factory” technologies. By deploying sensors and other connected devices throughout their factories, manufacturers can collect vast amounts of data that they can use to improve efficiency and quality control. Additionally, smart factories can help to address supply chain challenges by providing visibility into the production process.
As a result, the adoption of smart factory technologies will continue to grow in the years to come. However, some challenges also need to be addressed, such as increased processing capacity across longer distances with higher reliability.
Current standards limit accurate data transmission across a range of about 10m and require discrete cables for data, control, and power harnessed by a complex connector panel. Multi-function cables provide a hybrid solution with cleaner architecture, unlimited by copper distances.
Robotics
Like smart factories, many US manufacturers are also increasing their use and investment in robotic technology. This trend is fueled by supply chain challenges that are causing manufacturers to re-shore operations back to the US, using robots to offset the current shortage of available factory line labor and as a means to reduce their overall labor costs making them more competitive.
Although robots in manufacturing most often conjure images of one-armed machinations welding car parts, one of the fastest-growing opportunities is in the area of Robot Process Automation (RPA).
This sector is revolutionizing supply chain and logistics by automating manual tasks currently being carried out by human workers, such as data entry and report generation. RPA is also applied to Enterprise Resource Process (ERP) systems to streamline business processes.
With these robot-connected sensors distributed across the supply chain, production line, warehouses, and distribution centers comes an immense amount of data, all needing to be transmitted and powered from their remote locations to a potential knowledge center. From there, it will be collected, analyzed, and turned into actionable insights improving productivity and efficiency.
Other new industrial applications include Autonomous Mobile Robots (AMRs), such as delivery drones and automated picking/packing and material handling robots. Then, of course, there is the question of who or what is taking care of all these robots. Well, you guessed it, more robots designed to perform their own diagnostics using more sensors and data analysis to determine when they need to be taken out of service for maintenance.
The data and power cables needed for these applications also need to account for the rugged mobility proficiencies they will need to possess and the physical environments they will endure. Power and data supplies under these conditions will need to handle potentially dusty and dirty atmospheres, support more weight, and potentially millions of rolling or torsional flex movements without failing. Active optical hybrid cables and flexible printed circuitry are currently available data technologies that can meet these additional challenges.
Machine Vision
One thing that has made robotics such a growing trend is their superhuman sensor capabilities afforded by machine vision technology. Robots are now equipped with high-resolution cameras, microphones, heat sensors, and more, allowing them to not only sense what an item is but also interpret what to do with it.
Market research indicates that the demand for 3D machine vision has accelerated in tandem with the growing robotics trend. 3D machine vision allows vision-guided robots to take over specific tasks such as picking, material handling, assembly, and inspection.
Jerome Taylor, a Nortech Applications Engineer, also noted that “in almost every factory, you’re seeing the deployment of more camera systems for monitoring, more sensors, and more and more data collection.”
“Machine vision cameras have gone from one megapixel to 12 megapixels, and the frame rates have increased from 30 to 60 to 120 frames per second.” This is indicative of the increase in data quantity and the speed at which it needs to be reliably transmitted.
The medical field has exploded its use of this technology as well. Camera systems are being introduced into the operating theatre providing displays of the procedural area locally and engaging other surgeons off-site.
Some health facilities mount cameras on a patient’s head during an MRI, so that if that patient moves, the movement can be accounted for, resulting in enhanced image quality.
Augmented reality as a result of machine vision is another example of the growing number of applications in the healthcare field. One example is a system designed to detect the heat signature of blood flow and highlight it on a patient’s arm, making injection administration easier. Similarly, cameras, augmented by machine vision, recognize what they see and relay additional information to the healthcare worker in real time.
The commonality between all the examples above is the need to transmit more data more reliably across further distances while taking up less space. Rugged multi-function cables with hybrid power and data delivery in a small form factor will fill this need.
If you are working with any of the manufacturing trends outlined above, contact Nortech Systems to see how we can help you meet the next generation of data and power transmission requirements without today’s current space and distance limitations.