Flat Cable Solutions: Integrating Shielding and Reliability
As our world continually demands smaller, faster, and more powerful electronic systems, the anchoring components within these innovations must evolve in kind. For electronics engineers working within the aerospace and defense industry, the integration of flat cable solutions is an important component of the overall design. These flat, molded cable assemblies are redefining what’s possible in terms of design flexibility, and often an overlooked aspect is how shielding, and reliability are seamlessly woven into these solutions. Flat molded cable assemblies are composed of conductors enclosed within a flexible rubber material, like polyurethane or silicone, in a flat shape. Usually, one or two layers are arranged parallel in a thin and wide layout.

The Unseen Heroes of Modern Engineering
Underneath the sleek exteriors of our high-tech gadgets and aerospace devices, there exists a labyrinth of cables, each serving as a vital vein within the body of the system. Often, the unsung heroes of these systems are flat cables — thin, wide, and flexible, allowing for innovative design and packaging within a confined space. However, their significance in the grand scheme of electronic design far exceeds their slender profile.
The Anatomy and Benefits of Flat Cable Solutions
Designed with a parallel arrangement of conductors enclosed in flexible materials, flat cables provide more than just a connection; they offer a solution that adapts to the rigors of modern electronics.
Flex in More Than One Way
Unlike traditional round cables, flat cables offer a bending flexibility in a single plane, essential for designs that require high movement or tight spaces. This adaptability allows for creative routing and the ability to conserve space within the system, a feature highly prized in industries marked by ever-shrinking technological boundaries. Nortech can design flat cables to change planes to become three dimensional flexible cables. They can be configured to fit into tight spaces and transition from flat to round and back. Very thin molding walls can be provided to minimize thickness and width. The flexible polyurethane or silicone molding over the conductors provides ruggedness and environmental sealing. Flat molded cables can be used in place of rigid-flex PCB’s for interconnection.
Toughness in a Thin Package
Embedded within the flat cable is a story of resilience. The molding over the conductors isn’t purely for aesthetics. It ensures the ruggedness required to withstand the challenges of daily use, especially in mission-critical applications where any system failure could have catastrophic implications.
Shielding: The Silent Guardian
In the narrative of electronic components, shielding plays the role of the silent protector, defending against an invisible enemy: Electromagnetic Interference (EMI). Shielding is particularly critical in current applications where devices are densely packed and the risk of cross-talk and signal degradation is high. EMI shielding can be provided as overall shielding or individual wire/cable shielding.
A Balancing Act of Strength and Size
As we’ve established, flat cables have a natural inclination towards a slim and trim profile, ideal for compact systems. However, incorporating effective shielding into this geometry presents a unique set of challenges. Engineers must navigate the delicate balance between providing robust protection and maintaining the necessary form factor.
Shrouding the Signal
Several innovative techniques and materials offer viable solutions for the shielding of flat cables. From silver-filled conductive coatings for overall EMI shielding to individual wire/cable shielding setups, the array of options is as diverse as the applications that necessitate them.
The Solid Base of Reliability
In the constrained spaces of modern electronics, reliability is non-negotiable. A system is only as strong as its weakest link, and flat cable solutions with integrated robustness set an uncompromising standard for dependability.
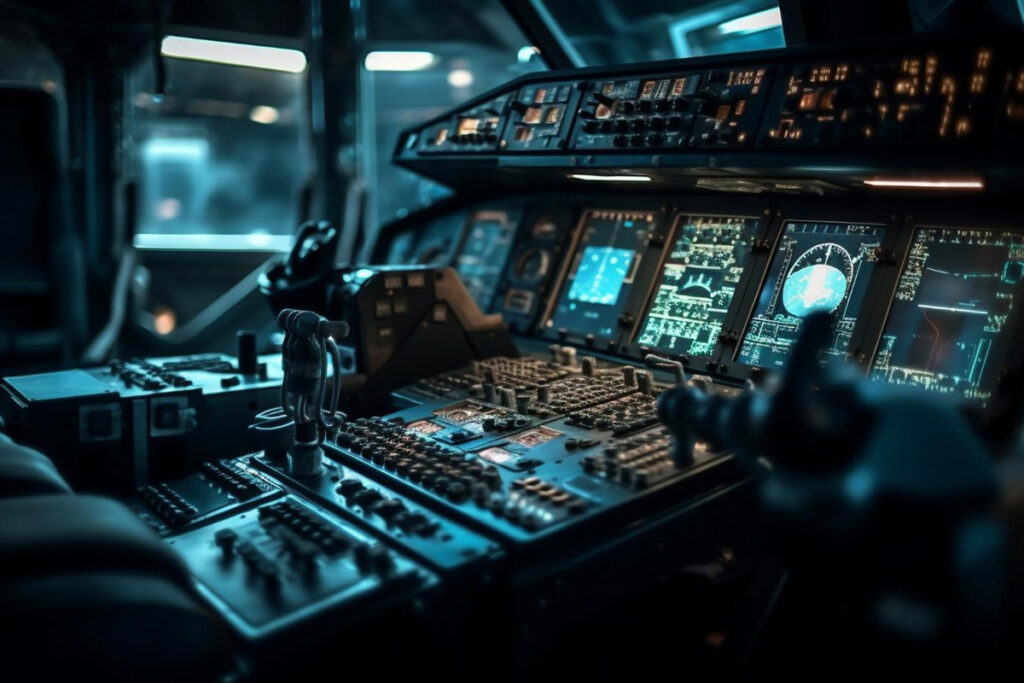
Factors that Test Fortitude
The road to reliability is paved with various factors that can potentially impede the performance of flat cable solutions. Stress on joints from excessive bending, vibration in aerospace applications, and even something as innocuous as dust can lead to wear and tear, ultimately reducing the lifespan of the system.
Fortifying Against Failure
The journey to fortify against these potential points of failure is marked by promising strategies. Careful selection of materials, such as ultra-flexible wires, and the incorporation of protective sheaths are just the beginning. The real testament to reliability lies in the meticulous testing and quality control processes that manufacturers employ to ensure that their flat cable solutions can weather any storm.
Embracing the Shield and Forge of Reliability
As we conclude our exploration into flat cable solutions, it is evident that the integration of shielding and enhanced reliability is no longer a luxury but a necessity. By embracing these advancements in electronic design, industries can not only solve current challenges but also proactively meet the demands of future technologies.
As connectors of the future take shape in our collective imagination, it is the integration of these auxiliary features that will set the benchmark for the new normal in electronic design. The shielded and reliable flat cable weaves within it the promise of a more connected, safer, and efficient world.
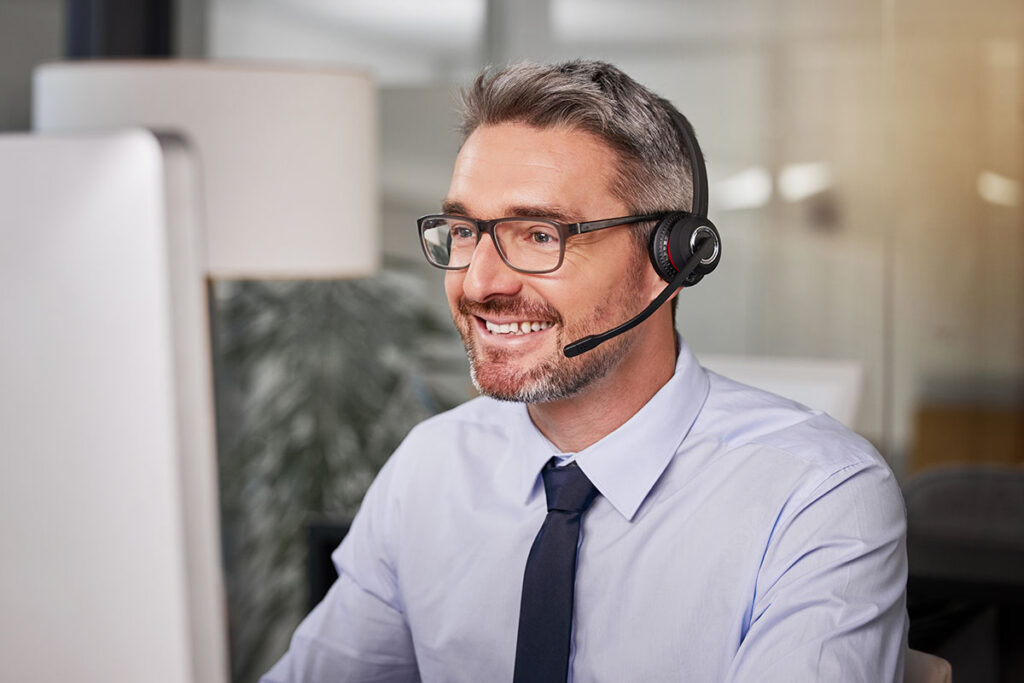