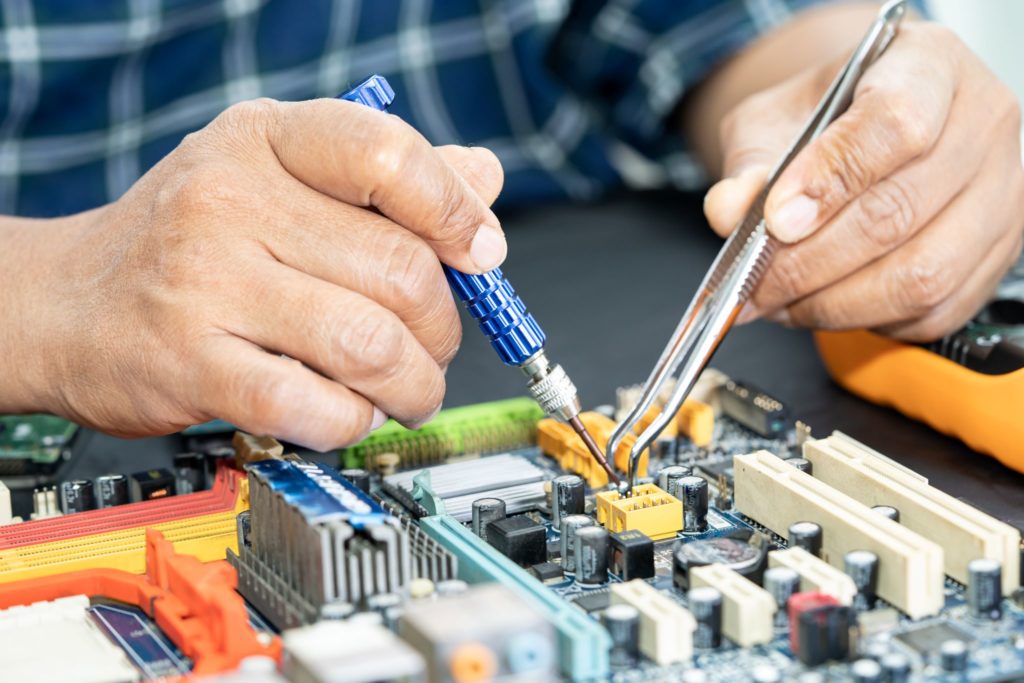
Developing a new product is a complex and dynamic process that requires the collaboration of multiple stakeholders, including engineers, designers, suppliers, and regulatory bodies. One key to successful new product development is managing suppliers effectively, ensuring they meet the required quality standards, cost targets, and delivery schedules.
This guide will outline five phases of new product development and provide tips for strategic supplier management throughout each phase.
Development Phases
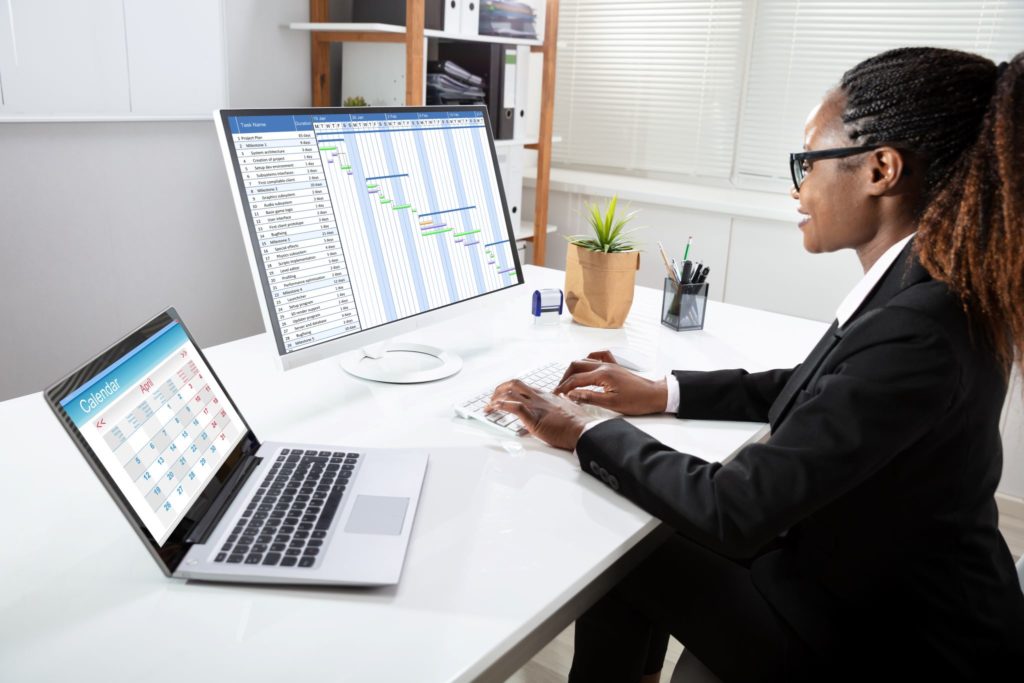
Phase I: Concept Development
The initial stage of new product development is known as the Concept Development phase. During this phase, the principal elements of clinical/marketing input, design feasibility, and user needs are established, and the process can begin by reviewing customers or marketing requirements, which serves as the foundation for developing concepts and models.
Engineers often want the freedom to design concepts and models by sourcing unique parts from unconventional sources such as big box hardware stores or auction sites in order to concentrate on the product’s overall functionality without being constrained by cost or component availability considerations. However, procuring parts from these sources is not feasible as the concepts and models must undergo feasibility analysis, technology evaluation, IP review, and regulatory compliance assessment to ensure their viability.
Managing suppliers in this phase typically involve reviewing the current suppliers of the concept components to determine if they are on a list of approved suppliers who already meet the necessary criteria for a reliable, cost-effective long-term relationship.
If existing suppliers are not on the approved list, Nortech’s supply chain team will coordinate the expansion of the list or recommend alternatives.
The goal is to source from approved suppliers to ensure the components and materials used in the concept prototype meet the necessary quality and cost standards.
Phase II: Planning and Architecture
In Phase II, create a project plan. Conduct a risk analysis, and determine the technical and regulatory requirements. The requirements document should be finalized, and critical suppliers informed of any changes or updates.
It is important to engage with suppliers during this phase to ensure that they have the necessary capabilities and capacities to meet the requirements and deliverables of the project. A regular review and communication process should be established to ensure that any changes or updates are communicated promptly and effectively.
Phase III: Detailed Design Development
Next, in Phase III, utilize the design inputs to develop design outputs. These design outputs become the basis of the Device Master Record (DMR) and are initially released. Here, the focus shifts from conceptualizing the product to refining the design. The goal during this phase is to ensure that the product design is not only functional but also manufacturable in the long term, with a focus on optimizing its manufacturing processes to ensure that it can be produced at scale, consistently, and cost-effectively.
Having well-established and functional working partnerships with approved suppliers is crucial in moving the design closer to the production stage, especially when considering supply chain risk management best practices.
Phase IV: Test Verification and Optimization Documentation
Phase IV, design verification takes place, and the design outputs from Phase III are evaluated for conformity against the design inputs from Phase II. A pre-production build is performed, and product verification tests are conducted. After verification, all documentation in the Bill of Materials (BOM) is moved to production control.
During this phase, suppliers must ensure that the components and materials used in the pre-production build meet the necessary quality and cost standards. Nortech’s program management and supply chain team will maintain regular communication with suppliers to ensure they are aware of changes or updates to the BOM.
Phase V: Validation and Launch
In the last phase, Phase V, perform a production build for clinical trials. After a final clinical report and risk analysis report is completed, regulatory approvals are obtained, and a market release plan is utilized.
At this point in the process, cost competitiveness is an influential factor but not the only consideration in choosing a final supplier. It is crucial to evaluate the supplier’s ability to provide the necessary components and products with consistent quality and at the desired price to ensure reliability and long-term viability.
Medical Device Considerations
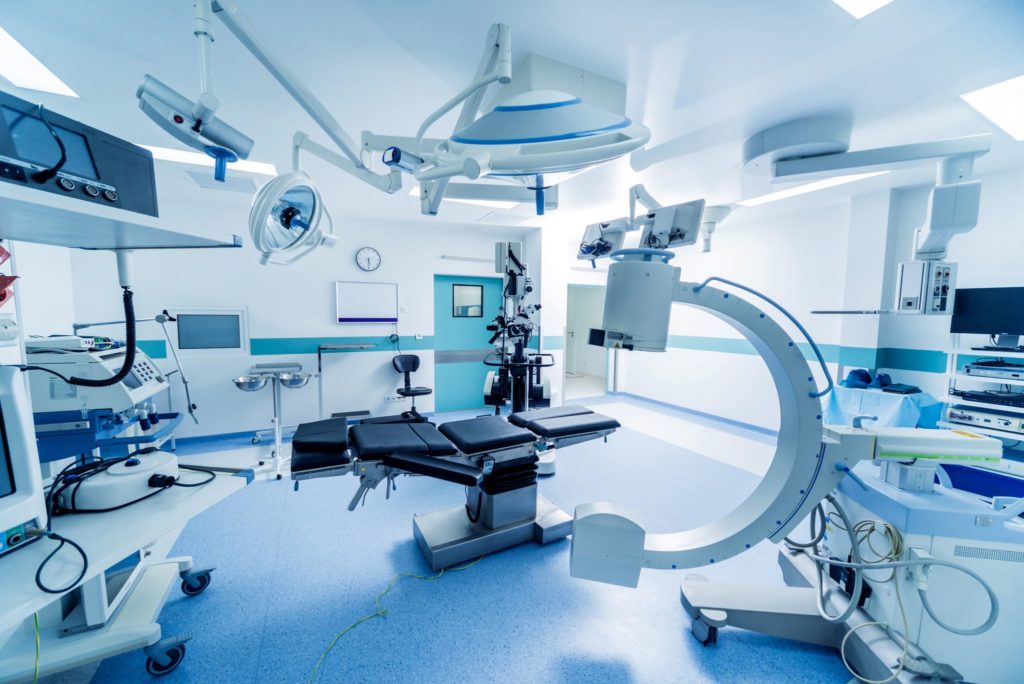
The development and production of medical devices are subject to stringent regulations and standards due to the critical nature of their use. The components and materials used in the design of these devices must meet these standards, and supplier management plays a crucial role in this regard.
Regulatory standards require traceability of the components and materials used in the design to ensure the safety and effectiveness of the medical device. The manufacturer must demonstrate that these components meet requirements and standards, such as dimensional, strength, and material requirements. As a result, it is common for medical device manufacturers to have a well-established and reliable supply chain with suppliers who have been approved, as it provides a higher level of assurance that the components used in the design meet regulatory standards.
How Program Management Can Help
Keeping customers informed of supplier management progress, timeline tracking, and budget status through effective program management can lead to numerous benefits. The program manager can establish trust and transparency by providing regular updates and promoting better communication and collaboration between all parties involved.
This frequent and complete communication can minimize confusion and prevent potential issues from arising, ultimately leading to a smoother and more successful project outcome. Additionally, by staying ahead of potential roadblocks, program management can proactively address any challenges and adjust plans as needed, ensuring that the project stays on track and within budget.
Maximize the success of your new product development by partnering with Nortech Systems for effective supplier and program management. Our practices, including early supplier engagement, regular communication, and close collaboration throughout each phase, guarantee that components and materials meet necessary quality and cost standards, resulting in a successful launch on time and within budget. Join us today to experience seamless communication and cost-efficient solutions.