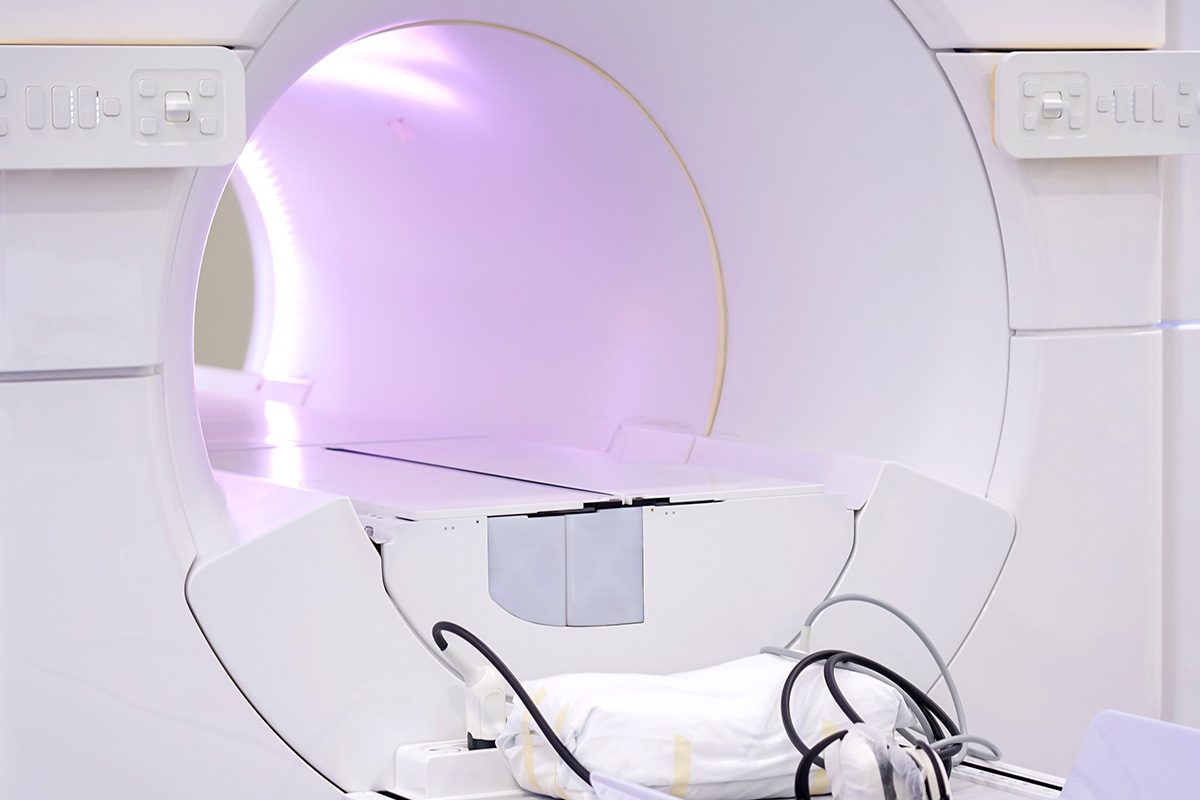
From Reactive to Proactive
The Future of Manufacturing with Fiber Optic Sensors
The manufacturing landscape is undergoing a digital transformation, and fiber optic sensors are at the forefront. Embedded within machinery, robotics, and dynamic electro-mechanical systems, fiber optic sensors are lightweight, space-saving, and electrically transparent. Fiber sensors are commonly used to detect subtle environmental changes such as vibration, temperature, pressure, density, and strain, as well as many other extrinsic and intrinsic variables. Fiber sensors transmit data as light signals, which are immune to electromagnetic interference, making them ideal for electrically noisy environments. With machine learning and artificial intelligence providing analysis, these sensors can quickly identify abnormalities and inefficiencies in performance and make recommendations for system maintenance or directly initiate change in real-time. Using fiber optic sensors and transitioning from reactive to prescriptive maintenance, manufacturers gain a significant competitive edge:
- Reduced Costs: Prescriptive maintenance minimizes downtime and unnecessary repairs, leading to significant cost savings. Performing maintenance only when it is necessary and focusing on the most critical equipment and tasks, prescriptive maintenance reduces overall service cost.
- Improved Product Quality: Real-time monitoring ensures consistent product quality at all stages of a product build, reducing defects and enhancing customer satisfaction.
- Enhanced Safety: Early and reliable detection of issues prevents accidents and safeguards workers.
Electronics Manufacturing Service (EMS) providers, like Nortech Systems, cater to demanding industries such as industrial, medical, and aerospace & defense. In these industries, minor system inefficiencies can have severe consequences to system performance and customer quality. Fiber optic sensors offer powerful solutions to support high-quality products.
Industrial:
- Ensuring Component Reliability: For Industrial product applications, monitoring potential failures in high-stress industrial equipment safeguards product quality and ensures product longevity throughout its lifecycle.
- Optimizing Robotic Systems: It’s no mystery robots will be a big part of our future. Robotics are already rapidly growing in our production industries. Real-time data generation and analysis on robot performance allows for prescriptive maintenance and can dramatically improve manufacturing efficiency and value.
- Enhancing Safety Protocols: Fiber optic sensors can detect overheating or abnormal vibrations, minimizing safety hazards for workers. Keeping employees safe is a top priority for dynamic monitoring technologies.
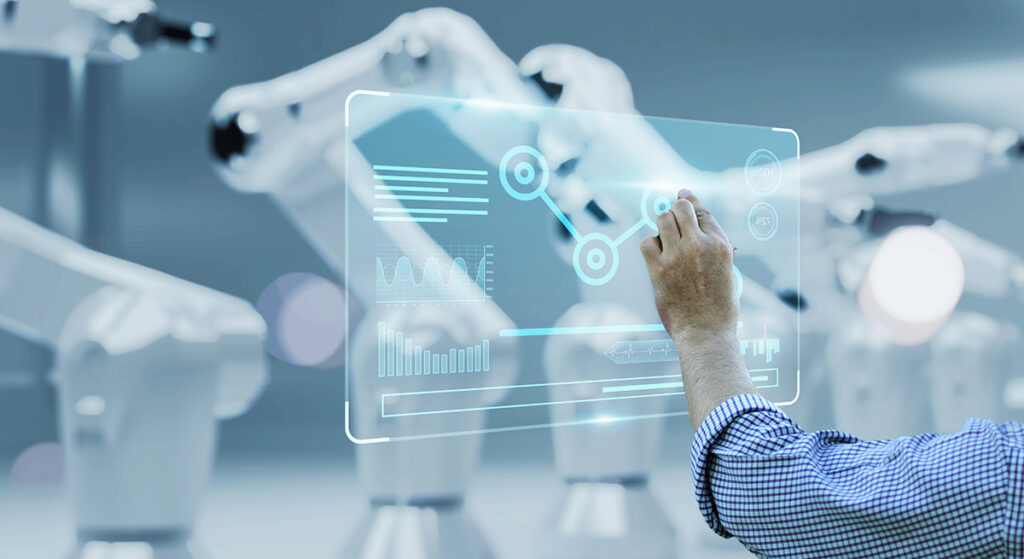
Medical:
- Maintaining Life-Critical Devices: Fiber sensors proactively address potential issues in medical equipment, ensuring patient safety and device reliability in the long run.
- Ensuring Sterility in Cleanrooms: Fiber optic sensors can monitor temperature and humidity fluctuations, crucial for maintaining sterile environments and ensuring proper operating conditions for sensitive medical devices and equipment
- Optimizing Production of Medical devices: Real-time data on equipment performance allows adjustments to ensure consistent quality and therefore more reliable procedure results
Aerospace & Defense:
- Guaranteeing Component Integrity: Fiber optic sensors can detect and address potential failures in critical aerospace and defense electronics before failures compromise mission safety.
- Monitoring Harsh Environments: Fiber optic sensors are ideal for high-vibration and extreme temperature environments common to aerospace applications. Sensor data can help engineers identify and refine achievable device performance in demanding aerospace and defense applications.
- Streamlining Production Processes: Predictive maintenance based on sensor data reduces downtime and optimizes production of vital industry components. For manufacturers, downtime and quality escapes are the enemy. Traditional preventive maintenance schedules can be wasteful, interrupting production and incurring unnecessary costs by performing maintenance either too early or worse yet, too late. Fiber optic sensors and real-time data analysis usher in a new era of prescriptive maintenance – anticipating issues before they cause problems.
In the realm of monitoring critical machinery, the use of real-time data to keep a constant eye on essential components like pumps, bearings, and motors is invaluable. This proactive and versatile approach to maintenance prevents unexpected failures and ensures machinery operates smoothly while eliminating service waste and inefficiency.
Quality assurance is another area where advanced technology plays a pivotal role. Through the deployment of fiber optic sensors along production lines and other dynamic systems, anomalies can be detected early on, ensuring only products and system performance meeting the highest quality standards reach your end customers. This not only safeguards the manufacturer’s reputation but also reduces costs associated with discarding defective products.
Lastly, optimizing energy consumption is a critical concern for manufacturers looking to reduce overhead and increase sustainability. By closely monitoring equipment and system performance, manufacturers can pinpoint inefficiencies and identify opportunities to save energy, leading to significant cost savings and a reduced environmental footprint.
By partnering with Nortech to harness these innovative approaches, our customers can significantly enhance their operations, reduce costs, and improve their customer value, positioning themselves as leaders in the competitive manufacturing landscape.